Understanding Porosity in Welding: Discovering Causes, Results, and Prevention Strategies
As professionals in the welding market are well conscious, recognizing the causes, results, and avoidance methods connected to porosity is essential for attaining robust and trusted welds. By delving into the origin causes of porosity, examining its destructive effects on weld quality, and checking out efficient avoidance strategies, welders can enhance their expertise and skills to generate top quality welds constantly.
Common Root Causes Of Porosity
Porosity in welding is mostly triggered by a mix of variables such as contamination, improper shielding, and insufficient gas insurance coverage during the welding procedure. Contamination, in the form of dust, grease, or rust on the welding surface area, produces gas pockets when heated, leading to porosity in the weld. Inappropriate protecting happens when the protecting gas, commonly used in processes like MIG and TIG welding, is not able to fully shield the molten weld swimming pool from reacting with the surrounding air, causing gas entrapment and succeeding porosity. Additionally, poor gas insurance coverage, usually because of wrong circulation prices or nozzle positioning, can leave components of the weld vulnerable, allowing porosity to develop. These variables jointly add to the formation of spaces within the weld, weakening its honesty and possibly causing architectural concerns. Comprehending and resolving these typical causes are essential steps in avoiding porosity and making sure the quality and strength of bonded joints.
Impacts on Weld Top Quality
The existence of porosity in a weld can substantially jeopardize the general high quality and honesty of the bonded joint. Porosity within a weld produces voids or cavities that weaken the structure, making it much more vulnerable to cracking, deterioration, and mechanical failing.
Moreover, porosity can prevent the performance of non-destructive screening (NDT) methods, making it challenging to detect various other defects or stoppages within the weld. This can bring about substantial security issues, especially in critical applications where the architectural integrity of the bonded components is vital.
Prevention Techniques Summary
Given the destructive influence of porosity on weld quality, effective avoidance techniques are important to maintaining the architectural stability of bonded joints. Furthermore, selecting the proper welding criteria, such as voltage, existing, and take a trip speed, can help minimize the danger of porosity formation. By including these avoidance methods into welding methods, the incident of porosity can be substantially minimized, leading to more powerful and more reputable welded joints.
Importance of Proper Shielding
Correct shielding in welding plays an essential role in avoiding atmospheric contamination and guaranteeing the honesty this content of welded joints. Protecting gases, such as argon, helium, or a mixture of both, are commonly made use of to secure the weld swimming pool from responding with components airborne like oxygen and nitrogen. When these responsive aspects come into call with the warm weld swimming pool, they can cause porosity, bring about weak welds with reduced mechanical residential properties.

Poor shielding can result in different defects like porosity, spatter, and oxidation, jeopardizing the structural honesty of the bonded joint. Sticking to proper protecting techniques is necessary to generate high-grade welds with minimal flaws and make certain the longevity and dependability of the bonded components.
Monitoring and Control Techniques
Just how can welders properly keep an eye on and regulate the welding process to make sure ideal results and prevent flaws like porosity? By this article constantly keeping an eye on these variables, welders can determine variances from the suitable conditions and make immediate adjustments to prevent porosity development.

In addition, executing proper training programs for welders is vital for monitoring and managing the welding process efficiently. What is Porosity. Enlightening welders on the importance of maintaining regular specifications, such as proper gas securing and take a trip rate, can assist avoid porosity issues. Normal evaluations and certifications can also guarantee that welders are skilled in monitoring and regulating welding processes
Moreover, making use of automated welding systems can improve monitoring and control capacities. These systems can exactly regulate welding parameters, decreasing the probability of human mistake and making sure constant weld high quality. By incorporating sophisticated tracking technologies, training programs, and automated systems, welders can efficiently monitor and manage the welding procedure to minimize porosity issues and achieve premium welds.
Verdict
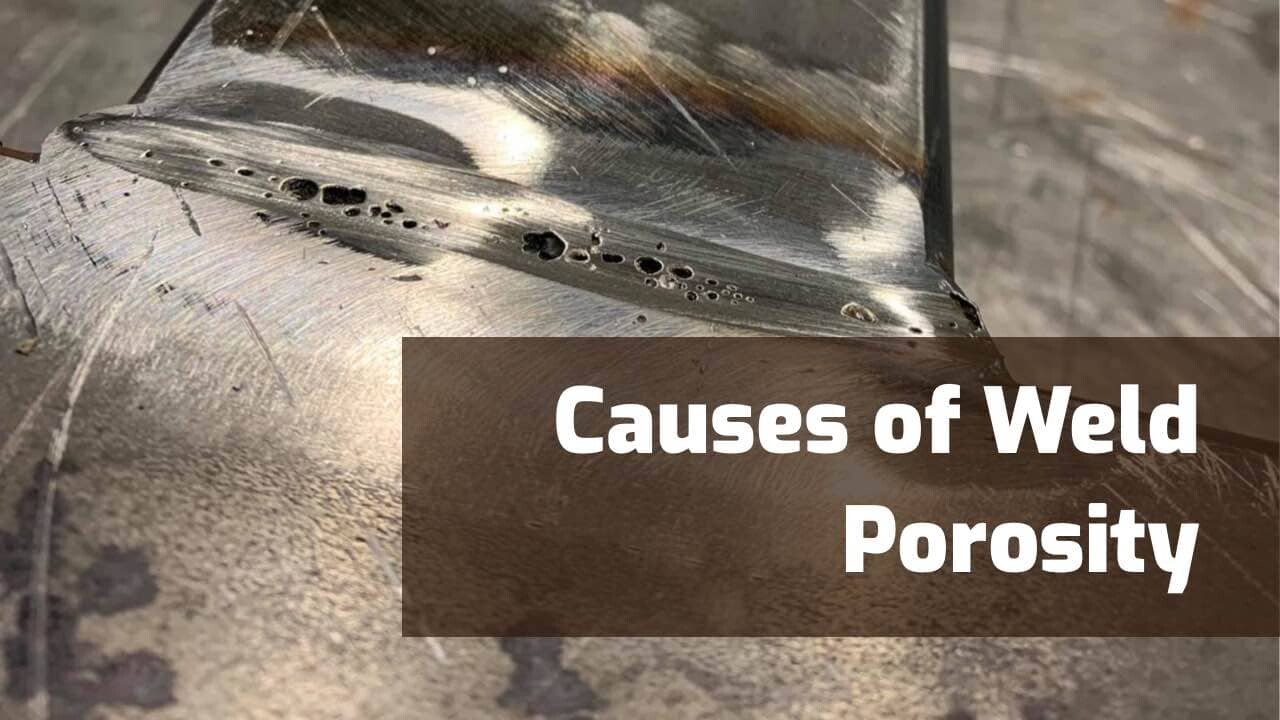